PLASMA TECHNOLOGIES HAVE MANY USES
Atmospheric pressure plasma surface treatment facilitates surface preparation prior to bonding, painting, varnishing or cleaning – which has led to a rapid expansion of its use in all industrial sectors.
Here below are some examples.
Please do not hesitate to contact us to discuss your projects – whatever materials or industrial processes you are planning on using.
AcXys Technologies has the expertise and experience to offer solutions that are easily integrated into your production lines to meet your specific requirements.
Main applications for atmospheric pressure plasma treatment
Plasma treatment will not only remove organic residues on the material surface, but also add new chemical functions that will drastically increase surface wettability for glues, inks, paints and varnishes.
This treatment is also an effective way to reduce the use of chemical compounds – more than often sources of environmental pollution (COVs).
The materials suitable for an efficient plasma treatment are incredibly various: metals, glass, paper, cardboard, polymers (Polypropylene, polycarbonate, polyethylene, PVC…), composite materials…
Surface cleaning and decontamination
Treatment with atmospheric plasma is an efficient and effective way to finish clean materials’ surface as it removes thin layers of organic or oil-based molecules.
For example, water-soluble oil residues found on aluminium surfaces can be removed within seconds thanks to plasma cleaning. Treated parts are almost immediately available for the next steps.
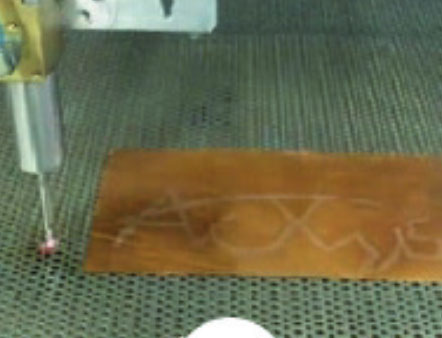
Copper oxide reduction
Plasma activation prior to bonding
This surface treatment will change the nature of the interface failure : from adhesive, the sealing becomes cohesive hence reaching high breaking strengths.
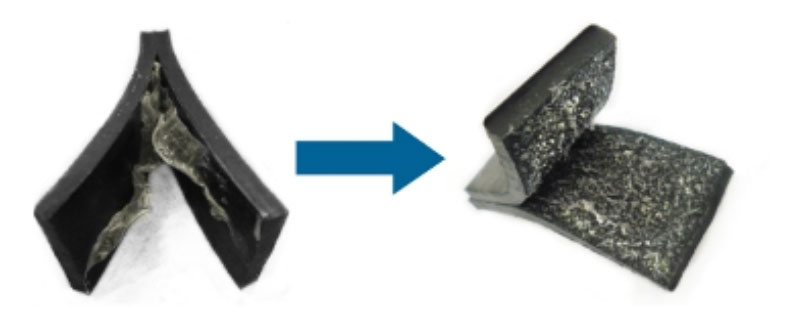
Left: easy adhesive failure
Right: cohesive failure
Plasma activation prior to injection moulding
In order to reach its full potential and technical objectives, operating injection moulding on a material requires a flawless adhesion of the upper layer onto the under layer.
Atmospheric plasma treat allows greater flexibility and can be used on an extraordinary variety of materials and shapes – a simple solution that is compatible with fast moving production lines and over-moulding procedures.
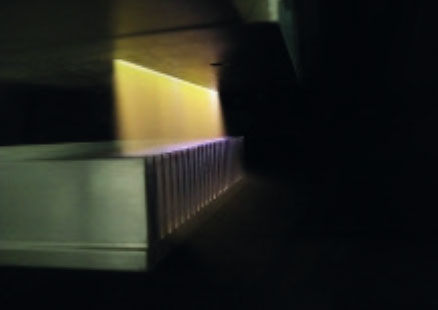
ULD plasma activation on aluminium prior to an overmoulding procedure
Plasma activation prior to marking and decorating steps
While acting on wettability and increasing adhesive capacities, a plasma treatment is key to improving printing quality, and reducing both ink use and embellishing substances used on glass or polymer.
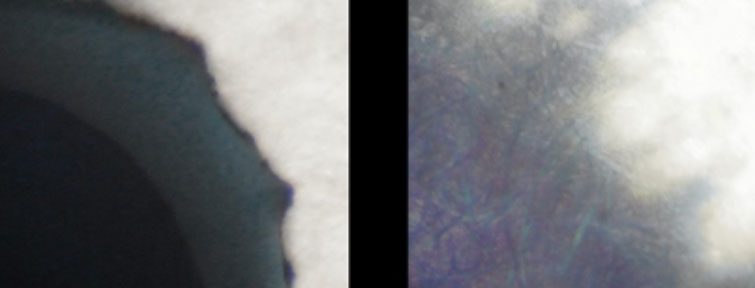
Microscope view of a drop on paper before and after plasma treatment
Plasma treatment prior to painting or varnishing operations
Plasma treatment will alter the surface of materials to be painted or varnished, hence increasing adherence of applied products but also dramatically enhancing the final output.
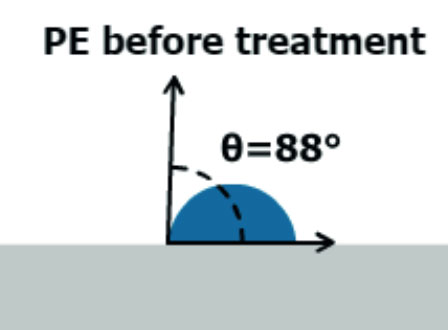
Variation of the contact angle of a drop on polyethylene before and after treatment
Thin layer deposit
Injecting a carefully selected precursor into plasma will lead to the formation of a homogeneous thin layer that will deposit onto the treated surfaces.
When conducted in an atmospheric pressure environment, the CVD (chemical vapor deposition) will be generated at low, or room temperature – on any material.
Atmospheric plasma process enables material deposits on plastic, composite, metal or glass surfaces.
Applications for this process are numerous– and sometimes remain little researched. Deposited layers onto materials open new areas for enhanced functionalities.
Silica deposit (SiOx) is now a well-known and attractive process to consider for the following applications:
- To apply an amines-based primer layer (NH2)
- To add optical features
- To add an anticorrosive layer on metallic surfaces
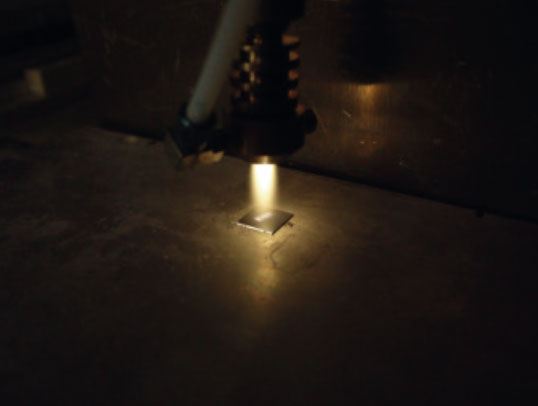